Pests are organisms that damage or interfere with crops, livestock, and human health. Control methods include prevention – keeping pests from occurring, suppression – reducing their numbers to an acceptable level, and eradication – destroying them.
Professional pest control technicians are trained to understand the specific types of bugs that live in your area. They also have access to more powerful treatments than you can buy at the store. Contact Pest Control Maine now!
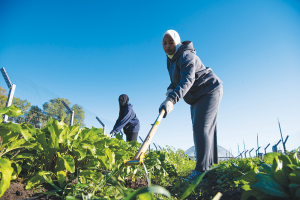
Pest identification is the first step in controlling pests. It helps you know what kind of pest you have and what preventive measures are needed. It also allows you to develop an integrated pest management (IPM) plan that reduces or eliminates the pest without the use of harmful chemicals. Pests can be plants, animals or organisms such as fungi and bacteria. They can be insects with six legs or arthropods such as beetles, ants, and wasps; mites, ticks and spiders; or nematodes, microscopic roundworms that live in the roots of some plants and are parasitic on other plants.
Pests enter homes and other buildings for food, water, shelter or to reproduce. They also damage property or destroy crops and affect people’s health by spreading diseases or contaminating food. For example, cockroaches and mice spread diseases that cause sickness, and their droppings contaminate food and trigger asthma attacks in children and adults.
Properly identifying the pest makes it possible to find out what it needs in order to survive and thrive. This information can help you control the pest by eliminating its habitat or removing its food source or other conditions that contribute to its growth and survival.
Identifying the pest is easy to do by looking at its size, shape and color; how many legs it has; and whether it has wings or antennae. You can then check online or in print for the pest’s description, life cycle, habits, threats and controls. If you are not sure, contact your local UC Cooperative Extension office to ask an expert for assistance.
Once you have identified the pest, you can determine what preventive steps are needed to reduce its numbers to unacceptable levels. For example, to keep cockroaches and mice from entering homes, remove their sources of food, water, and shelter. Store food in sealed containers, repair leaky pipes and caulk cracks and crevices, and make sure garbage is removed regularly. Use roach baits and other products to control them if the problem persists. Carpet, cigar and drugstore beetles can be controlled by removing or blocking access to their breeding materials.
Identifying the Source of the Problem
Pest control involves eliminating unwanted organisms, such as insects, rodents, and weeds. The purpose is to protect the environment, human health and property from these organisms, which cause damage or interfere with desired activities. Pests also pose a threat to the environment because they degrade the quality of plants, soil and water. In addition, they can trigger allergies and asthma attacks in humans. Rodents, for example, chew wood, furniture and food. They carry bacteria like plague, hantavirus pulmonary syndrome, salmonellosis, and leptospirosis, which can be spread to people. They also cause a lot of damage to crops and buildings.
Identifying the source of the problem is one of the first steps in pest control. Usually, the goal of pest management is to keep populations below threshold levels. Threshold levels are based on economic, aesthetic, or health considerations. For example, the presence of a single rodent in a food processing facility forces action. In homes, the presence of rats or cockroaches triggers a number of health concerns including skin allergies and asthma attacks.
The most common methods of pest control are prevention, suppression, and eradication. Prevention is the best way to minimize pests, but it is often difficult. It requires observing and monitoring pest activity, identifying and using the right type of bait or trap, and maintaining good hygiene to avoid contamination.
Suppression is the goal of controlling pests after they have been detected. The right combination of controls can reduce a pest population to an acceptable level and prevent it from building up again to unacceptable levels.
Chemical pest control involves using chemical products that kill or repel pests. These products can be applied directly to the target pest or to the environment in which they are living. Generally, the safest and most effective products are those that have low risks of exposure to children or pets when used according to label instructions.
Integrated pest management (IPM) is the practice of combining appropriate pest control tactics into a plan to reduce pests and their damage to an acceptable level without the use of unnecessarily harsh chemicals. The tactics may include biological control, cultural control, mechanical control and sanitation. Pesticides are only used when prevention and other control strategies have been exhausted. Relying on pesticides alone can lead to development of resistance and may harm other organisms at the treatment site.
Developing a Plan of Action
An integrated pest management (IPM) plan uses a series of techniques to keep pest populations at bay. These techniques can be natural or chemical, and they are based on preventive rather than reactive approaches to pest control. This approach is often less disruptive to plants and animals than more aggressive control methods.
The first step in the IPM process is to determine which pests are causing unacceptable harm, such as damage to crops or property, or to human health. This is known as establishing an action threshold. Generally, it is determined that the number of pests must be reduced below this threshold to avoid unacceptable harm. This threshold is based on esthetic or economic considerations, and may be influenced by the age of the plants or structures affected.
Once an action threshold has been established, monitoring procedures are implemented to keep track of pest numbers. This can be done through trapping or scouting for insect, insect-like, mollusk and vertebrate pests; visual inspection for weeds; or analyzing environmental conditions like temperature, moisture, light levels and plant growth. This information can help you predict when the pest population will reach an action threshold, so you can take action before the problem worsens.
Identifying the pest is crucial for any type of treatment, and identifying the type of pest will guide your choices regarding what control tactics to use. Proper identification will enable you to select the most effective control strategies and reduce the amount of pesticide or other treatment required. Recording all pests identified will also aid in tracking your progress and determining what corrective actions are needed.
In most cases, controlling pests is necessary to ensure the safety of humans and pets. However, this can be difficult, as some types of pests cause harm without being noticed. These pests often live in the ground or under surface debris, where they can be difficult to find and treat. They can also hide in major home systems or appliances, which can lead to costly repairs and voids on the homeowner’s home warranty coverage.
An effective plan for pest control will include prevention and suppression, as well as eradication. Prevention includes steps to stop the pests from becoming a problem by changing their environment, such as clearing out habitat or blocking access to food and water sources. Suppression involves reducing the pest population below an acceptable level to avoid damage or loss and keeping it there with regular treatments. Eradication is used only when the damage caused by the pest is unacceptable.
Implementing the Plan
In order to implement the pest management plan, it is necessary to have a system in place to document all actions taken. This includes creating checklists for all pest inspections and treatments that include all the details of the site, date, type of pesticide used, etc. This will help to ensure that the correct actions are being taken to keep the facility pest-free.
A key step in implementing the pest control plan is to set action thresholds. This allows managers to take action only when the pests reach a level that poses an unacceptable risk. This is a key feature of Integrated Pest Management.
The final step in implementing the pest control plan is identifying the right method of pest control. This may include the use of physical barriers to block pests from entering or using baits and traps to capture them. It can also involve the use of mechanical or biological solutions.
Physical barriers are a common and effective method for preventing pests from entering structures. This can include sealing cracks and crevices to prevent rodents or insects from entering, installing screens on doors and windows to allow air circulation while blocking insect or rodent entry, and using sticky traps to catch bugs and other pests.
Biological pest control is the use of a pest’s natural enemies such as predation, herbivory, parasitism and pathogens to reduce pest populations. This can be done by introducing natural predators, parasitoids or pathogens into the environment or by augmenting the natural population through large-scale releases of these organisms.
Chemical pesticides are often a last resort and should only be used when all other methods of control have failed. They can be effective in controlling some pests but have drawbacks such as environmental risks, nontarget effects and resistance development. Integrated pest management seeks to reduce dependence on these chemicals but recognizes that there will be some pests that can only be controlled with the use of chemical controls.
Pests can cause a lot of problems for your business, including damage to your equipment and buildings. In addition, they can lead to food contamination. They can also trigger allergies and asthma attacks and spread bacteria that can cause diseases like Plague, Hantavirus Pulmonary Syndrome, Lassa fever, Salmonellosis and Leptospirosis. To help protect your business, it’s important to implement a pest control program that can prevent and treat any infestations as quickly as possible.