A patio provides a location for parties and relaxation. Whether it is hot summer or cold winter, it offers an outdoor location free from bugs and mosquitoes.
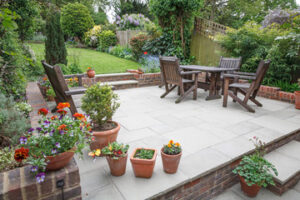
When building a patio with paver stones or bricks set in concrete or with other dry-laid materials, builders follow similar marking, excavation, tamping and leveling processes. Visit https://www.cleanstoneconstruction.com/ to learn more.
A patio is a great way to extend your living space into the yard and take advantage of views that may be limited by existing trees, bushes or landscape elements. However, before the patio can be built, the ground must be excavated and framed to prepare it for concrete installation. This is a critical step in any hardscaping project and requires skilled professionals to complete it safely and correctly.
Before digging, a professional will map out the location of the patio using a line level. They will then use a piece of graph paper or an online floor planning tool to create a to-scale plan of the site. Once they have finalized the design, the area is marked off and excavation begins. The excavation process will likely involve digging down to a depth of 7 inches — 3 inches for the gravel base and 4 inches for the concrete.
After the excavation is completed, a layer of loose gravel is placed on top of the soil. This is followed by a layer of sand. This provides a base for the pavers and helps to reduce shifting of the surface as it ages. A layer of mulch can also be added to the sand for aesthetic purposes.
A wood frame is constructed on the excavated site, either using 2 x 4 pressure-treated ground-contact lumber or a more flexible bender board that can be manipulated to accommodate curves in the patio design. Before the concrete is poured, the frame is soaked down with water to prevent the mix from drying out too quickly. Then, a portable cement mixer is loaded with the concrete mixture and mixed for the amount required to fill one grid unit of the patio (4 inches thick). The concrete is poured into the frame and tamped with a hand tamper or power tamper.
Sub-Base
In order to properly support a paving slab or surface, it is important that there is a layer of sub-base underneath. Whether this is for a patio or driveway, the sub-base ensures that the load of the paving is spread evenly. This will help to prevent settlement and ensure that the paving performs well.
This can be done in a number of ways, depending on the type of material used. For a patio, we usually recommend an aggregate sub-base such as crushed stone certified and guaranteed as MOT Type 1. This is a strong, stable and durable material that also drains very well, helping to prevent water pooling beneath the paving which can cause damage and make surfaces slippery.
It is recommended that any material used for a sub-base is compacted as thoroughly as possible using a machine such as a vibratory roller. This will need to be done both longitudinally and transversely, where possible, until the material is ‘tight’.
Before starting construction, it is a good idea to make a to-scale plan of the patio to ensure that it is the correct size and layout. This can be done with graph paper or an online floor planning tool and will help to eliminate any surprises once the construction begins. It is also important to consider the direction that any water runoff should go, as this will help to prevent any flooding issues later on.
Once the ‘tight’ sub-base has been completed, it is time to start construction of the patio itself. It is often best to build this as a grid of 3-foot-square units, which can be either square or rectangular. These are framed with 2 x 4’s and nailed together using 8-penny galvanized common nails.
Forms
Patios can be made from a wide variety of materials, and new trends are leaning toward incorporating patio amenities that can make the area comfortable for dining, relaxing or entertaining. For example, a built-in fire pit can provide warmth and atmosphere, while a water feature can bring tranquility. Some people choose to add a pergola for shade or an outdoor kitchen to facilitate cooking and eating outdoors.
Most standard concrete patios are built using forms to hold the concrete in place, and there are several different types of forms available for this purpose. Some types include on-site wood slab forms, manufactured metal framing for walls and foundations and newer, energy-efficient insulated concrete forms.
Before the forms are put into place, they must be anchored to the ground. This is done by staking the corners of the square with 2×4 lumber and driving 3d nails through the lumber at each stake point to ensure that the concrete form will not shift. It is also a good idea to place 1x kickers at each joint and 4-foot intervals around the outside of the forms for additional support, since concrete is very heavy.
A patio can be constructed from a number of different materials, including bricks and paving stones. A paver patio is usually constructed from a grid of 3-foot-square concrete units that are framed by 2×4 lumber. For this type of patio, a gravel base is often used, particularly in areas that experience poor drainage or freezing temperatures. The builder will work in sections, pushing the concrete into the forms and removing excess concrete with a hand trowel. He may brush the surface of the concrete with a bristle broom or trowel to produce a textured finish.
Concrete
A beautiful concrete patio can make all the difference in a backyard living space. It’s a great place to entertain friends and family, relax and unwind, or simply enjoy the outdoors with your favorite book or glass of wine. However, patio construction is a specialized type of concrete work that requires proper planning and execution to achieve the best results.
A concrete patio can add significant value to a property, as well as increase its overall curb appeal. Many homeowners choose to use concrete for their outdoor spaces because it’s durable, visually appealing, and versatile. Concrete can be molded and shaped to create a unique design, and it can also be stained or colored with pigments to produce a variety of colors and hues.
Unlike wood and composite wood, concrete is highly resistant to rotting or warping. Additionally, it can withstand heavy foot traffic and heavy patio furniture without cracking or sinking. It also doesn’t need yearly staining or refinishing, which can save homeowners time and money.
Concrete is also environmentally friendly. It can be produced from recycled materials, and it’s durable enough to last for decades. This reduces the need for frequent replacements, which contributes to lower energy consumption and fewer greenhouse gas emissions.
Whether you’re looking to transform your existing yard or create a brand new patio, concrete is a good option. KC contractors say concrete patios have a longer lifespan and require less upkeep than decks, so it’s an excellent choice for homeowners who want to spend more time enjoying their outdoor space rather than worrying about maintenance. Concrete can also be used to build other features, including raised garden beds and retaining walls.
Pavers
Pavers are paving stones that come in different shapes, sizes, and colors to fit your patio design. They can be crafted from materials like natural stone, bricks, and concrete to offer durability and enhance aesthetic appeal without requiring extensive upkeep.
They are commonly installed over a gravel base that’s been spread out and tamped down to compact the soil. A board is often laid across the area to help determine that it’s level. A geotextile cloth is sometimes placed over the tamped down soil to limit weed growth. A layer of sand is then added, typically a coarse sand that’s been screened to remove fine debris. It may also be a polymeric sand that’s coated with an agent that helps to bond the sand and prevent it from shifting in the future.
Builders often use stakes and string to outline the area of the patio in advance. This method allows the builders to see what shape and size the patio should be and how it will lay out with the rest of your garden landscape. Alternatively, builders can use a type of eco-friendly spray paint to mark the shape and size of the patio ahead of time.
Once the builders have marked the area, they’ll start laying out the pavers. They’ll usually start with the largest stones first to provide a strong foundation. They’ll then work their way down to the smaller stones. Once all of the paving stones are in place, sand or a fixing material is poured on top and then brushed into the joints between each paving stone. It’s then watered in to lock-in the stones and create a sturdy surface that can be used immediately.