Mold is a dangerous parasite that can devour building materials and pave the way for dry rot. Regular mold inspections can prevent the problem from getting out of hand.
Mold testing can include air samples and surface swabs. The cost of a test can vary depending on the type of mold and whether it requires staining or culture testing. Contact Ace Mold now!
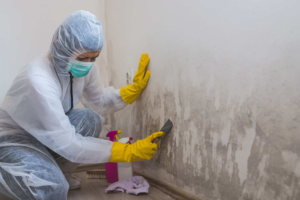
Mold inspection costs vary by region and the type of property being tested. Larger homes are typically more expensive to inspect because of the increased space that needs to be covered. In addition, if the inspector must use specialized testing methods such as air sampling or surface swabbing, this can also increase costs.
Before hiring a professional mold inspector, research companies. Read online reviews, check Better Business Bureau ratings, and collect estimates to find a company that fits your budget. Also, consider a company’s experience, knowledge of the industry, and licensing, which can be found through your state or municipality and on the company website.
A basic inspection generally starts with a visual examination of the property, checking for any obvious signs of mold growth. This may include mold stains on walls, ceilings, or furniture and damp spots in attics or crawl spaces. In addition, the inspector will test for moisture in the property and look for signs of water damage or leaks.
If the inspector finds evidence of a mold problem, they will recommend air or surface samples to be taken for analysis. Surface samples are usually taken with a swab or tape, and are sent to a lab for testing. This can be an inexpensive method, but it is important to note that a single sample does not provide the complete picture of the situation and additional samples will be required.
Air tests, on the other hand, are more comprehensive and give the inspector a clearer idea of what is occurring inside the home. These tests can be more expensive, but they are worth the investment for the peace of mind they offer.
Before the inspector arrives, you will need to prepare the property for the test. This includes removing any items that could block access to areas of the home, such as appliances and furniture. You should also turn off all ventilation and remove any clothing, including undergarments, that may be contaminated with mold. In addition, you should inform occupants of the house about the inspection and request their cooperation in providing unobstructed access to all areas of the property.
Preparation
Mold inspections can be expensive, but they’re essential for identifying hidden infestations. Mold spores can thrive in places that are difficult to access, and once they settle there, they can quickly grow into full-blown colonies. Mold inspectors know how to find the source of an infestation and provide remediation techniques that work for the type of mold growing in your home. They can also help you identify the difference between surface and structural mold, which is more difficult to remove.
Mold spores are usually airborne, but they can also settle on surfaces inside your house and grow into full-fledged colonies. Mold spores can also travel in the air and reach other areas of your home, which is why it’s important to get a complete inspection of your property. A trained professional can look behind walls, in plumbing fixtures, inside ceiling tubes, and underneath appliances to assess whether a problem is structural or only superficial.
One of the best things you can do to prepare for a mold test is to close any doors or windows in the room or area where you suspect that mold is growing. This will maximize the concentration of mold spores in that specific space, making them easier for an inspector to detect. It’s also a good idea to shut down any HVAC systems that are located in the affected area. This will prevent the system from circulating air and diluting any spores that are already in the air.
It’s also a good idea to remove any items that could block an inspector’s access, both inside and outside the property. This includes furniture and other items, as well as clutter around the property. Moisture is the key factor in most cases of mold growth, so it’s important to make sure that any sources of moisture have been addressed before an inspection.
When a mold inspector arrives, they will take several samples from different parts of the property, including air, surface, bulk material, and swabs. These samples will then be sent to a lab for testing and identification. They will be able to tell you what types of mold are present, their spore count, and whether the spores are alive or dead.
Types of Inspections
There are several different types of inspections available, depending on the specific needs of a property or building owner. These include visual inspections, air testing and surface sampling. The type of inspection required will largely depend on the type of mold in question.
A visual inspection will look for the most obvious signs of mold, including patches of discoloration and foul odors. The inspector may also use an endoscope to peer into tight spaces such as behind wall studs or under sinks. The inspector will try to find the source of moisture and work with the client to come up with a remediation plan.
Air testing will test the air for spores. The inspector will take one sample indoors and one outdoors to compare and create a baseline. This method can be more expensive than a visual inspection. However, it is important to note that outdoor samples can be affected by factors such as wind and rain.
Surface sampling is less invasive than air testing. The inspector will swab a suspected area of mold with a specialized tool. These swabs are then sent to a laboratory for analysis. The laboratory can determine the type of mold, its spore count and if it is toxic or non-toxic.
A specialized test can also be used to determine the presence of dangerous mold. These tests can be used to identify specific toxins such as fusarium or penicillium. These toxins can cause localized infections in the nails, cornea or skin. They are also known to trigger allergies and respiratory problems.
During the inspection, the inspector will try to determine how widespread the mold is. He or she will search areas that are known to be prone to water damage, such as the basement, attic and kitchen. The inspector will also check for hidden mold in places such as behind walls and inside of pipes.
Before the inspection, it is important to shut off all HVAC systems and remove any plants or other items that could be affected by mold spores. It is also recommended to avoid using cleaning and disinfectant chemicals for 48 hours before the inspection. This will help to stabilize the indoor environment and allow for more accurate testing.
Conclusions
Mold inspections can help prevent or limit the extent of property damage caused by mold. They can also protect the health of occupants. Mold can cause respiratory problems, allergic reactions and other medical issues. In addition, it can destroy the structural integrity of buildings.
Qualified professionals visually examine a property to detect signs of mold, water stains and discoloration. They may also use specialized tools to identify hidden moisture sources. In addition, they will take air samples and surface samples for laboratory analysis. In some cases, they will recommend a professional remediation to remove mold and prevent future growth.
The cost of a mold inspection depends on the type and quantity of mold found. A general inspection generally covers most molds, but you will likely pay more for an inspection that focuses on specific species of mold, such as Stachybotrys chartarum, or for a deep clean after flooding.
Molds can grow in a wide variety of conditions, including damp and humid areas. They can grow in wood, paper and other organic materials, and they can be spread by wind or carried through openings in walls, floors and ceilings. Molds are not limited to certain seasons or climates, and they can be found in homes, schools, offices and hospitals in any country.
Indoor mold spore concentrations are often higher than those of outdoor air. This is due to the fact that spores are released into the air more quickly when the humidity is high. Therefore, it is important to lower the humidity in a building before conducting a mold inspection.
When taking an air sample, it is important to use the same method of sampling in all rooms that are tested. The air pump should be set at the same flow rate, and the collector must be used for the same duration of time in all rooms. The collector should also be placed at the same height above the floor in all rooms that are tested. It is also important to make sure that the collection device is not contaminated by touch, smearing or other contamination.